Dongkuk Steel carries out eco-friendly policy for sustainable value creation.
Scrap iron is used as a recycling material in order to manufacture new steel products in the electric furnace based manufacturing way. All workplaces thoroughly follow the principle of minimizing pollutant emission and energy consumption. Dongkuk Steel makes its continuous effort to minimize environmental pollution and make the best-quality products through process improvement and equipment investment. .
Environmental Management Report
Green Management
Policy
1. We recognize the environment as an essential requirement of management, and consider it first in all steps.
2. We comply with domestic and foreign environmental laws and agreements, establish and fulfill high criteria to satisfy customers’ needs.
3. We pursue the efficient use of resources in all management activities and minimize environmental pollution through continuous improvement.
4. We find the potential possibility of environmental emergency and come up with organizational measures.
5. We establish the goal of achieving the environmental policy, announce this policy to stakeholders, and do the best to advance environmental management.
Green Management
System
Dongkuk Steel thoroughly performs system-based management in order to prevent the environmental pollution that can occur in production activity and to minimize damage. The company systematically manages environmental management items according to the Environmental Management System ISO14001, and established the Web System in interaction with site DB and DKMS in order for real-time sharing in the whole company.
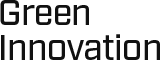
Eco Art Furnace was first introduced in Korea in order to maximize energy efficiency and reduce greenhouse gas emission.
- Energy saving through continuous injection and preheating of iron scrap
(energy consumption 30% ↓)
- Minimization of externally emitted combustion gas through the application of after-burning, and combustion tower burner
Hot Charge Production Type was introduced to increase energy efficiency through the flexible operation of heating furnace.
- Incheon Steel Plant No.1 Rolling Factory: introduced HDR (Hot Direct Rolling) in Sep. 2012
- After HDR, improved fuel efficiency 80% and reduced greenhouse gas emission by 35,000 tCO₂eq annually
Installation of Solar Power Generation Facility
- Installed 2.7MW solar power generation facility in Busan Factory in Oct. 2014
- Pollutants/Greenhouse gas emission “Zero” facility
- Expected to install 12.5 MW solar power in Dangjin Plant on in March 2021.
Application of Bio Boiler, a representative eco-friendly clean energy technology
- After the operation of the boiler with eco-friendly fuel in Aug. 2017, greenhouse gas emission reduced by14,000 tCO ₂eq annually.
RTO Regenerative Thermal Oxidizer
Fuel use reduction with process reuse through waste heat recovery
Heat Storage Heating Furnace
Introduced the heating furnace able to reduce pollutants and increasing energy efficiency through LNG fuel
LED Light Replacement
Energy saving by replacing factory lights, ceiling lights, street lights with high-efficient lighting devices
Installation of ESS Energy Storage System
Implemented eco-friendly corporate culture by actively supporting the government’s new energy projects and additionally installing heat storage incinerator
Installation of EMS Energy Management System
Real-time monitoring and analysis of power data for each facility is possible through the establishment of an integrated EMS in the Incheon plant